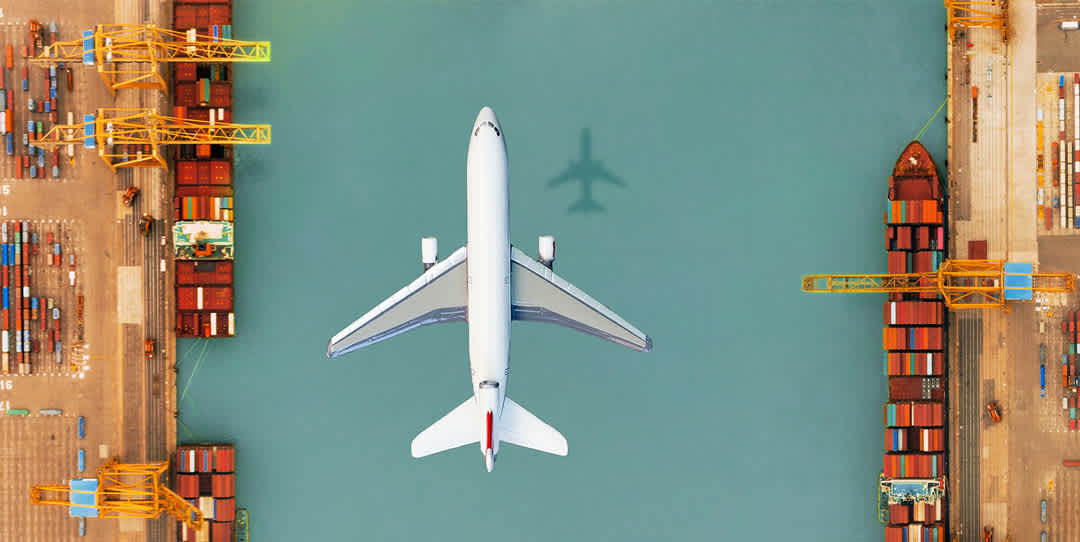
July 19, 2024
Navigating the Complex Supply Chain Disruptions Amid the Recent Global Tech Outage
A massive tech outage on Friday, July 19 has halted operations across multiple industries, grounding thousands of planes and throwing global supply chain operations into disarray. As of Friday afternoon, more than 37,000 flights were delayed globally, including more than 8,000 within the U.S. Over 4,000 flights were canceled, with more than half of these cancellations affecting U.S. routes, according to real-time flight tracker FlightAware.
The cause of this disruption was a software update for Microsoft Windows operating systems issued by the cybersecurity firm CrowdStrike. CrowdStrike said it has identified the issue and is actively working on a fix.
What are the implications for the air freight industry?
The impact of the CrowdStrike outage has been particularly severe on the global air freight market, at a time when demand for air cargo is outpacing supply. In June, air cargo demand was up 13% year on year, measured in chargeable weight, compared with supply growth of 3% year on year.
Impacting critical components of many essential systems, the outage has disrupted operations across the entire supply chain, affecting everything from booking and shipping to customs clearance and tracking. Major carriers with extensive global networks and heavy reliance on IT systems, such as Delta Air Lines, United Airlines, and Lufthansa, are likely experiencing the most significant challenges. The ripple effect could lead to disruptions across various industries “for days or even weeks to come,” said Thomas Kempf, Senior Director of Air Freight Business Development at Flexport.
Looking ahead, he acknowledged that the extent of the impact on air freight in the coming week will depend largely on how quickly CrowdStrike can restore full functionality to its systems.
“However, it is safe to expect ongoing disruptions and delays for at least the next few days,” Kempf added.
What disruptions to ocean freight operations are we seeing?
In the U.S., container terminals saw minimal impact, according to William Contessa, Ocean Procurement Manager at Flexport. However, at the time of incident, the outages limited operations related to specific container terminals: for those delivering or picking up laden or empty containers, operations sequences were abruptly halted.
Many of the impacted were able to rectify the issue and return to operations hours later with minimal disruptions. That said, some of those attempting to execute a pickup or delivery of a container at the port at the time of incident were unable to do so, and needed to come back later in the day (or another day altogether).
Ultimately, this means that some containers would require multiple pickup and delivery attempts at the container terminal, and may be assigned a different arrival date to the delivery location.
In Europe, the ports were only slightly impacted and have already returned to normal.
What should clients do to avoid delays?
Flexport is not impacted by the outage, and our systems continue to run as normal. We advise all businesses to maintain open communication with their freight forwarder. Be prepared for potential delays and disruptions, and consider flexible shipping schedules to accommodate unforeseen challenges. It's also advisable to prioritize critical shipments and provide as much advance notice as possible for booking and shipping.
Additional Tips:
- Stay updated on the latest news and advisories from airlines, ports, and customs authorities.
- Consider alternative transportation modes, such as ocean freight, if feasible.
- Build in extra time for shipments to account for potential delays.
- Maintain clear and open communication with all involved stakeholders, specifically suppliers and customers.
Related content
Emissions Calculator
Sustainability Starts with Awareness. Take the first step in building a greener future, measure your freight emissions today with Flexport.org's Open Emissions Calculator.
Flexport’s Vision
Celebrating One Year of Fulfillment: Flexport’s Vision for Building the Best End-to-End Logistics Solution
BLOG
Decarbonizing the Aviation Sector: Introducing Flexport’s Sustainable Aviation Fuel Program