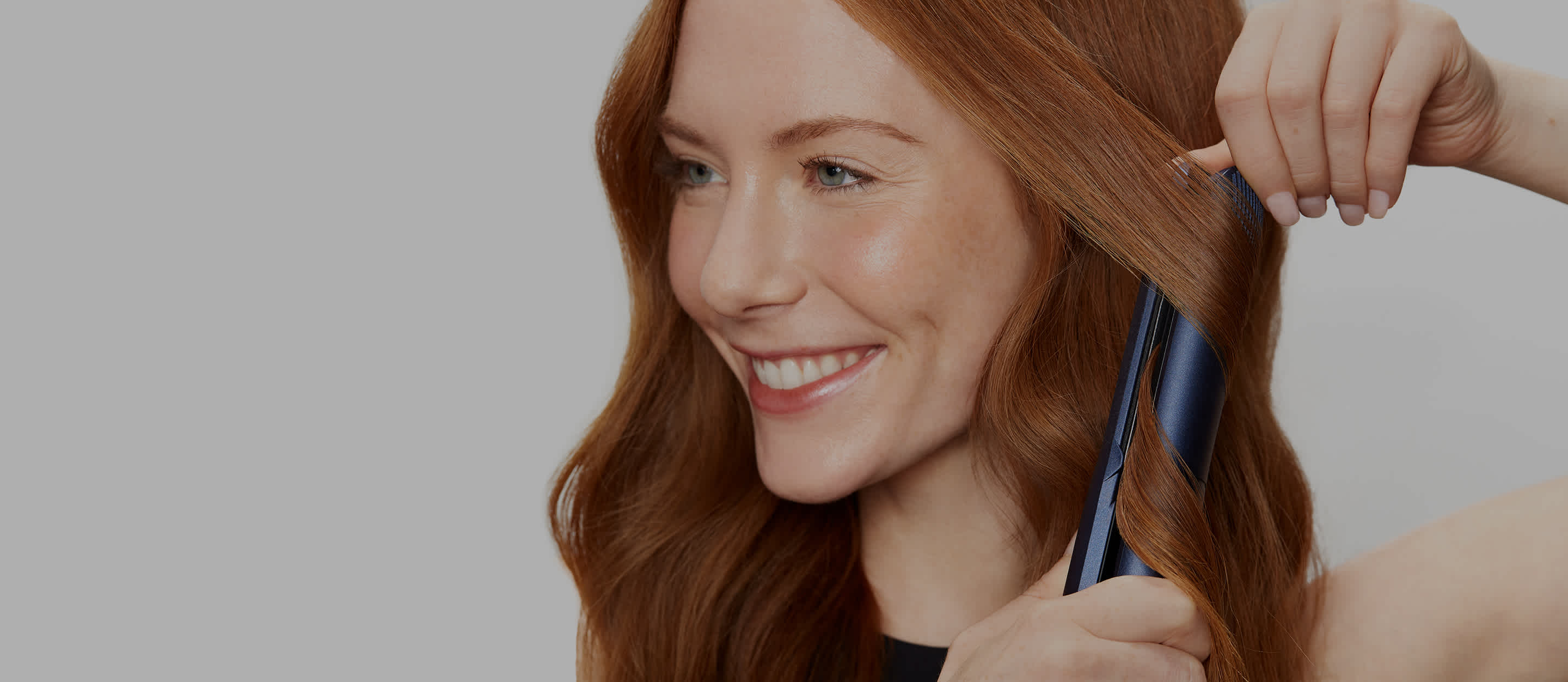
Consumer Goods
Ahead Of The Curve: How Cloud Nine Boosts Supply Chain Visibility And Employee Headspace With Flexport
Hours saved per week from tracking shipments and monitoring business KPIs
CLOUD NINE, the producer of award-winning hair styling products, relies on an efficient and effective supply chain to maintain stock and deliver key business KPIs. Fast access to accessible data makes this possible, while allowing people to focus on what matters.
The haircare and beauty product market is extremely competitive. For CLOUD NINE to meet customer demand and build brand loyalty for their range of straighteners, hair dryers, curling wands, and other accessories, effective supply chain management is essential. Running out of stock would have a knock-on effect, leading customers to purchase elsewhere, or to consider alternatives when it comes to important gift-giving moments such as Black Friday, Christmas, and birthdays.
Prior to working with Flexport, CLOUD NINE was only able to maintain their supply chain through often time-consuming and complicated processes. Implementing the Flexport platform simultaneously freed up the team’s time to spend on business-critical tasks while providing the comprehensive oversight needed to keep suppliers and partners informed and ready to react promptly to any challenges.
“Flexport allows us to be proactive by providing all the information we need in one place. It’s the perfect marriage of digital processes with a human touch,” said Lewe Goldmann, Supply Chain & Operations Director at CLOUD NINE. “It frees our team from time-consuming transactional tasks so we can spend time on priority areas—improving our visibility of shipments in the short-term, and ability to think strategically in the long-term.”
Making Time For Strategy And Planning
CLOUD NINE manufactures its products in South Korea, shipping them to the UK, Europe, Australia and New Zealand as part of a multi-faceted supply chain. As part of its sustainability goals, it does not use air freight. Having full visibility throughout the shipping journey is essential to keeping the process on track, and products in stock. But CLOUD NINE found that compiling the data to do this effectively was taking valuable time and focus away from using that data as part of critical tasks like forecasting.
The Flexport platform and its range of automated solutions saves CLOUD NINE’s teams 4 hours a week by drastically reducing the time spent pulling together the information they need to track shipments and monitor business KPIs.
"We want to be spending 80% of our time on the things that really matter", explained Lewe. "That's why as many shipments need to be hassle-free and automated, so that we can have the time and headspace - and Flexport allows us to achieve this.”
“It’s so much quicker for me to keep track of important business KPIs thanks to the reporting feature,” said George Sweeney, Supply Chain Manager at CLOUD NINE. “Collecting the relevant data to answer questions like ‘how cost-efficient is a specific shipment’ used to take upwards of an hour and involved several platforms. Now it can be done with one click of the download button.”
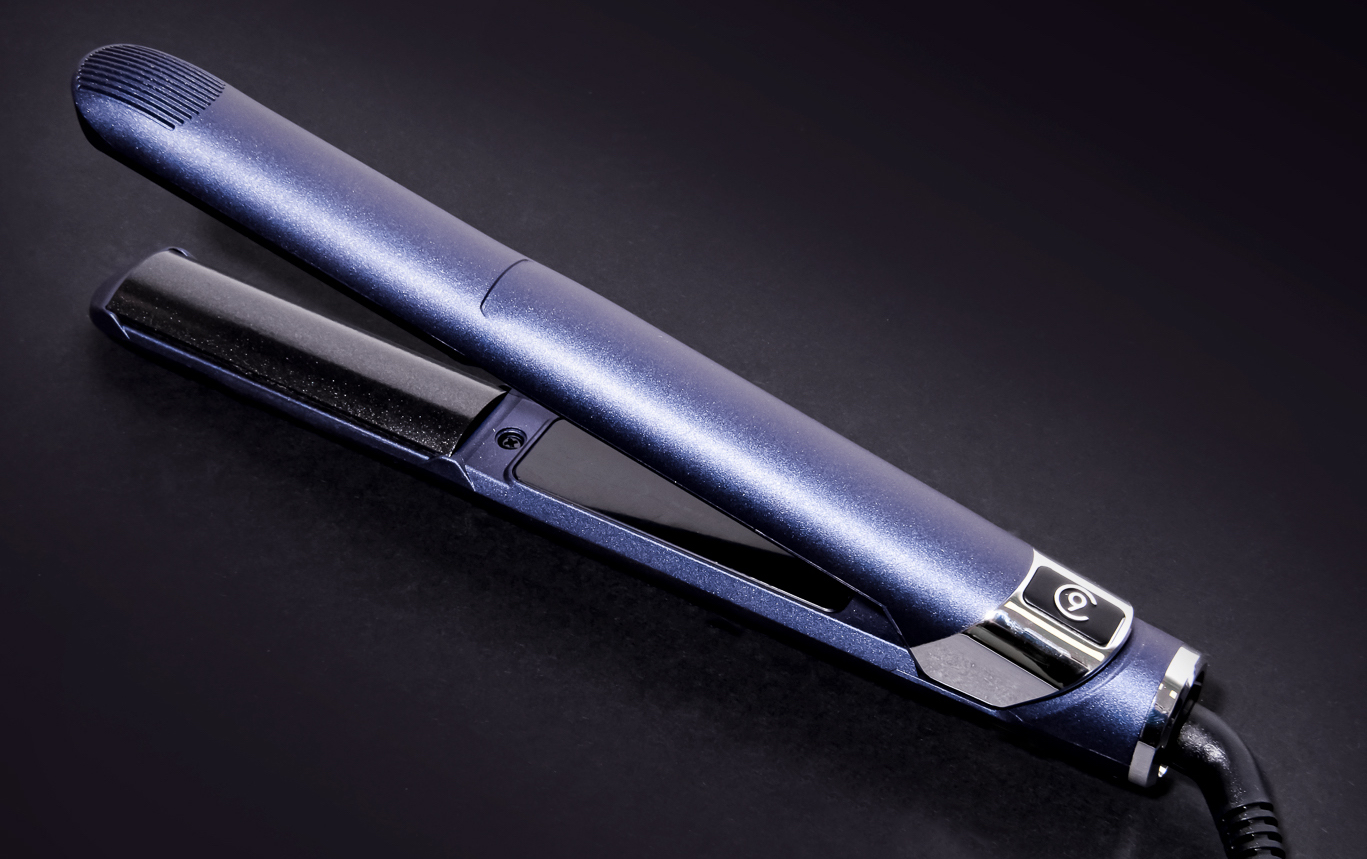
Increased Visibility And Flexibility
The ability to track containers across thousands of miles of ocean allows CLOUD NINE to accurately report on everything from expected delivery time to container utilization. The more visibility, the more precise they can be, and quicker they can react to unexpected issues such as bottlenecks. Before working with Flexport, CLOUD NINE could access this information only via labour-intensive methods and it often took several days to get. A faster solution was required.
“One of our biggest challenges in maintaining the supply chain is knowing what we need, and when," says Lewe. “With so many moving parts, there can be a lot of unpredictability. Flexport lets us stay on top of this by providing responses and information at speed so we can respond appropriately.”
A prime example of improved visibility is when tracking shipments in the Suez Canal. A notoriously busy passage, it is difficult to provide accurate estimates on arrival time until shipments have passed through. Previously, CLOUD NINE had to wait three to four days to receive confirmation that a ship had moved beyond the canal. With the Flexport platform, they can use the live map to instantly see when that has happened and reduce delays in booking warehouse locations.
"I have the habit of only trust the containers’ ETA (estimated time of arrival) once the ship is through the Suez Canal - with Flexport I can look it up myself if a ship has passed and don't have to waste time (mine and someone else's) to ask my Freight Forwarder for this info" says Lewe.
Being able to accurately track container fill vs container volume—making sure space is not wasted—has also helped CLOUD NINE ship more cost-effectively and sustainably by avoiding adding unnecessary containers to shipments.
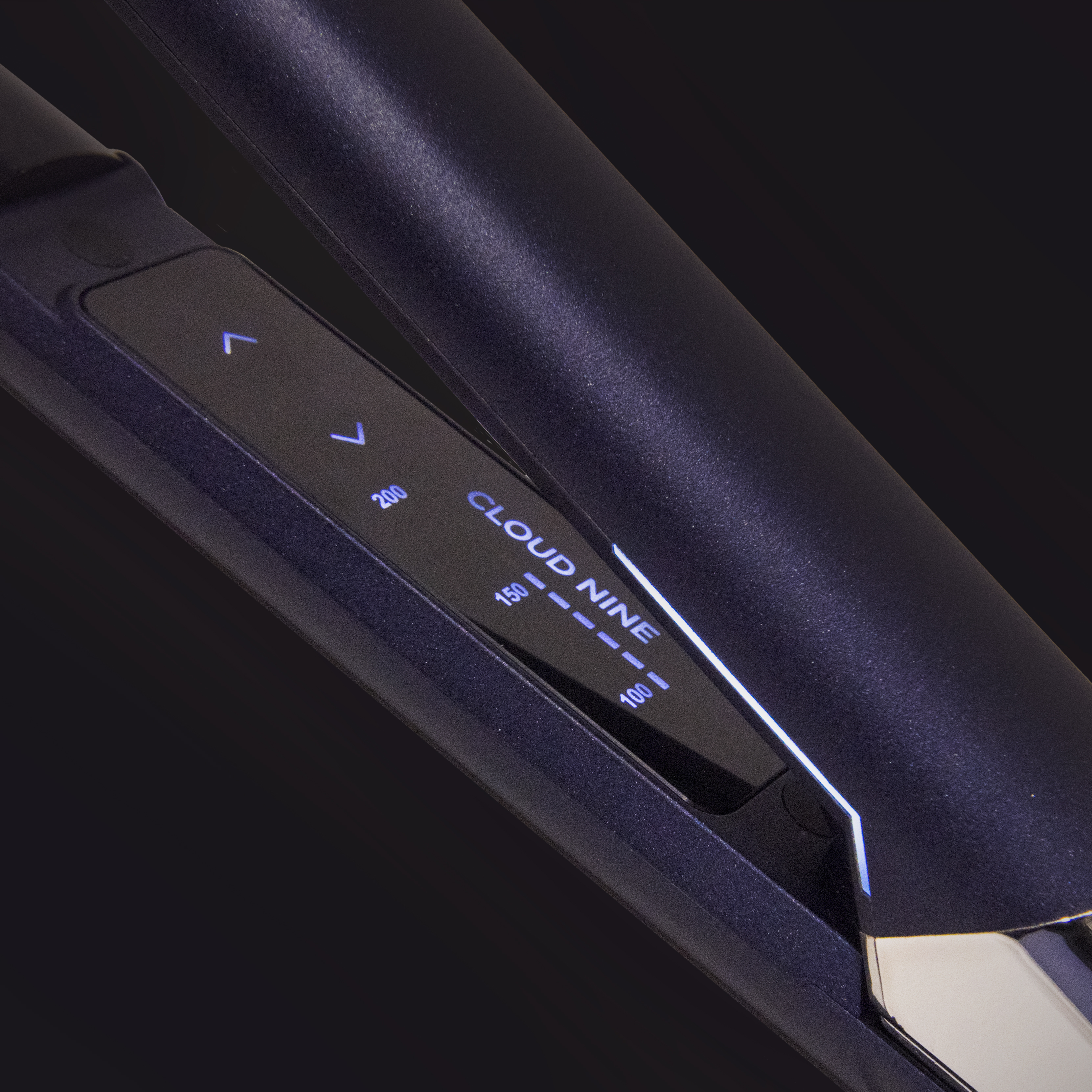
A Digital Solution With A Human Touch
Every supply chain is unique. For CLOUD NINE’s to run effectively, the technology and tools to track and maintain the process need to be malleable enough to meet the company’s specific needs. This meant finding a solution that combined technological precision with the flexibility that comes with a human connection and effective customer service.
“One of the first requests I made to Flexport convinced me we had made the right decision,” explained Lewe. “We have a special agreement for shipping containers in the UK. I expected this to take a significant amount of time to get signed off, especially given we had no trading history with Flexport as our freight forwarder. They solved it within a couple of weeks. It showed me Flexport was willing to go above and beyond to support us.”
Read More Customer Stories
Read on to find out how companies across sectors and industries are getting more out of their logistics by partnering with Flexport.


Consumer Goods
How Klean Kanteen Met Sustainability Goals and Saved 400+ Hours a Year on Reporting
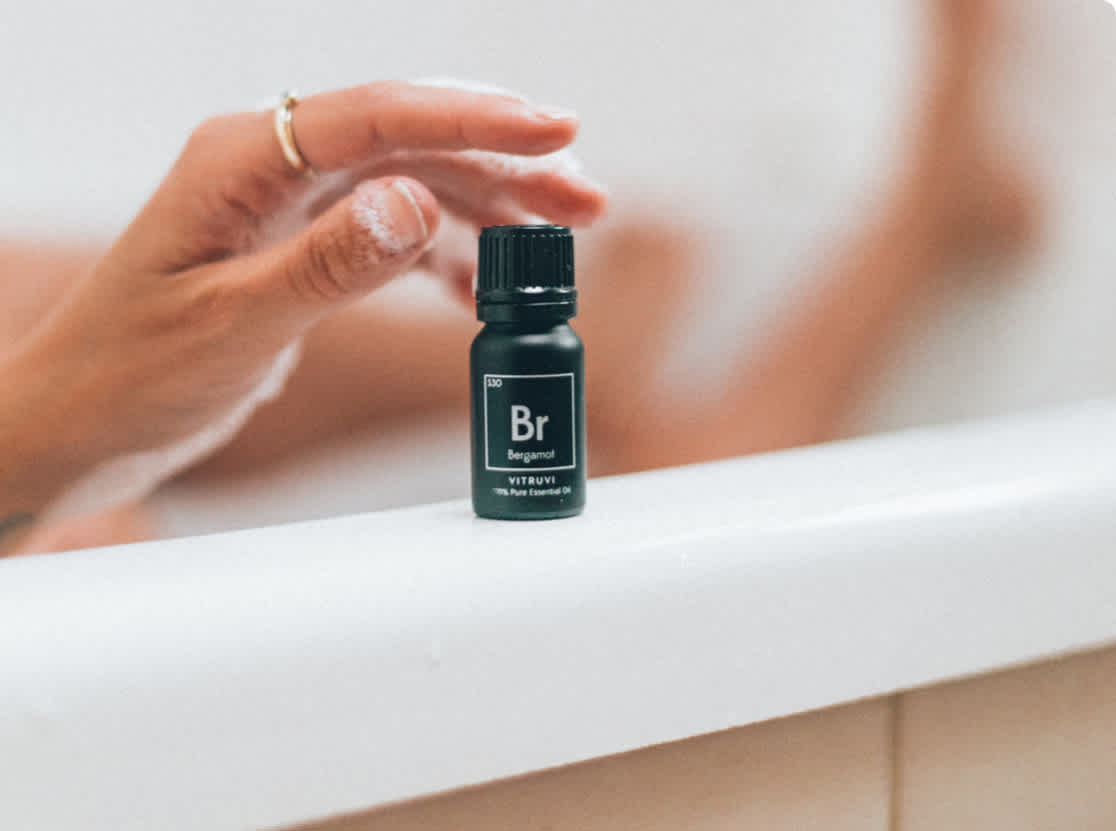

Consumer Goods
Luxury Wellness Brand Vitruvi Achieves 900% Growth in 4 Years With Flexport Capital
Ready To Get Started?
Talk to a supply chain solutions expert and see the Flexport platform in action.