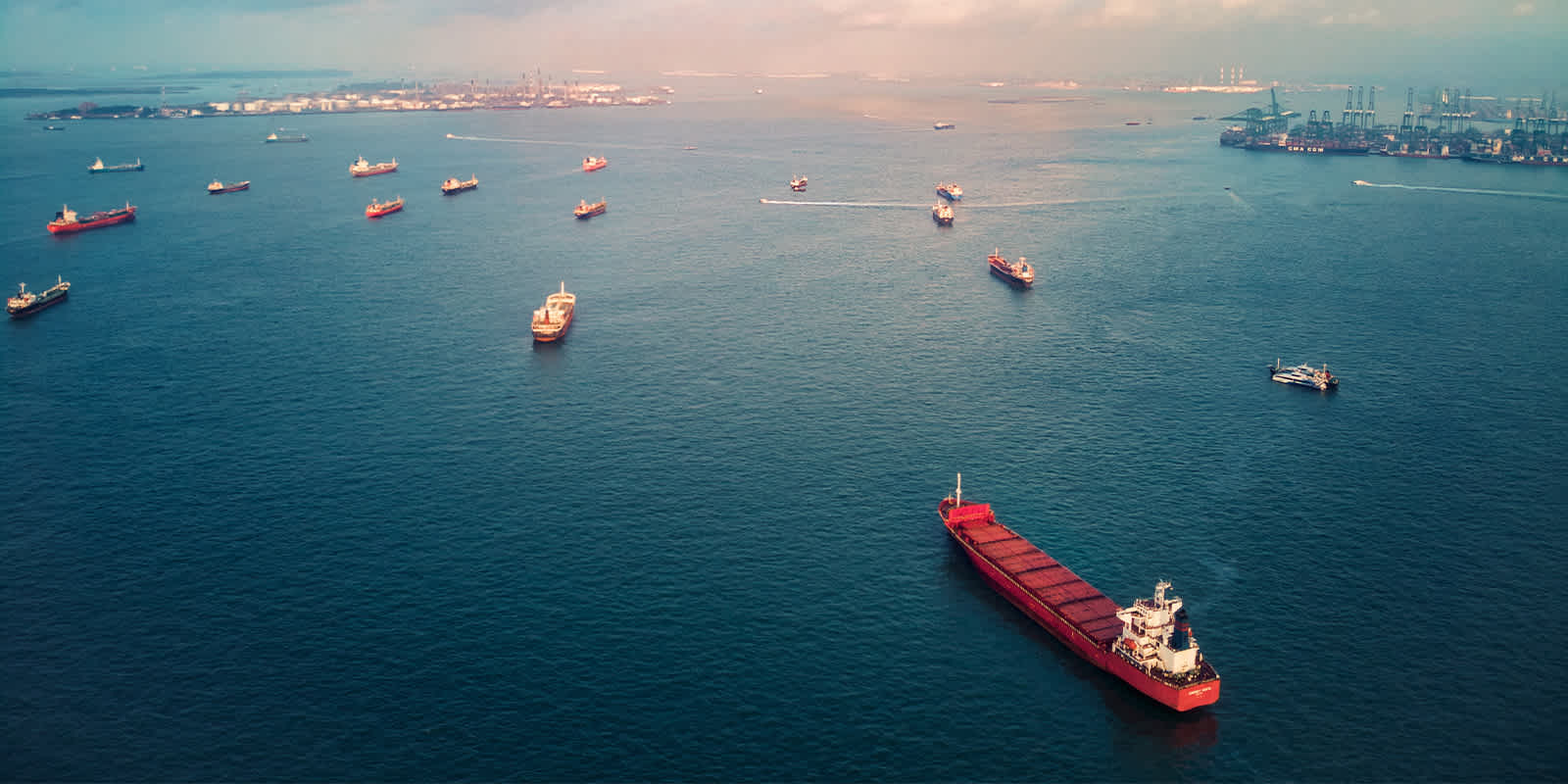
June 25, 2020
Pulling Off A Peel-Off: How to Shorten Lead Times Between Ocean and Trucking
Pulling Off A Peel-Off: How to Shorten Lead Times Between Ocean and Trucking
A well-timed logistics practice called a peel-off can shave days off transit times by streamlining the steps between a container’s arrival at a destination port and its departure for its next point, usually a warehouse or distribution center.
Coordinating a peel-off requires alignment between shippers, freight forwarders, and their ocean and drayage or trucking partners. The teamwork needs to be tight, but the potential for efficiency is extraordinary.
The approach, sometimes called a free flow, means containers are ready for pick up sooner, reach warehouses or other drop points faster, and require less overall labor to move. The key is reducing time at the terminal, no small feat in an era of congestion and volatility.
An Opportunity for Efficiency
A peel-off is available to shippers that meet volume minimums—or work with freight forwarders that do.
Required volume can range from 30 to 300 containers on a single vessel, depending on the port and its terminals. In some instances, the peel-off can include containers from multiple vessels.
A successful peel-off begins at the port of origin, with freight forwarders ensuring containers are stowed on the vessel or vessels in groups. Think of it as the “priority baggage” sticker you see at airports.
Once at destination, longshoremen remove the containers from the ship, segregating them in stacks in a staging area, usually a yard near the terminal. Since containers are already grouped for speed, a top picker crane moves them quickly, compared to the usual transtainer, also known as an RTG, which has a more limited range.
With a peel-off, freight forwarders know the day and time of recovery for every container before the vessel arrives, so trucks only go to the staging yard after the containers are organized, allowing more efficient delivery coordination or prioritization.
When trucks can free-flow into the yard—forgoing the short notice of the traditional appointment system—drivers regain control of timing, bypassing congestion, unpredictable wait times, and the limitations of access during peak hours only.
Supply Chain Teamwork
Achieving a clean peel-off is sometimes a matter of relationships as much as organization. That’s especially true when demand is urgent, congestion is pressing, or service level agreements leave no time for sluggishness.
This was the case for a manufacturer recently facing a sales surge due to COVID-19 stay-at-home orders. Flexport’s Ocean Team organized a peel-off that pulled the company’s containers from the vessel within 48 hours, against an otherwise expected window of six days.
In this instance, the terminal had a minimum requirement of 40 containers on the same vessel. The manufacturer had 31, but combined with other Flexport customers’ containers, the Ocean Team counted 50 total and quickly compiled a list of all containers to coordinate the peel-off with a trucking partner that stayed on task with the terminal.
Keen strategy won this one, but at its core, a peel-off is always a team effort, ensuring efficiency for everyone involved.
To learn more about how to organize a peel-off, reach out to your Flexport account representative or email hello@flexport.com.