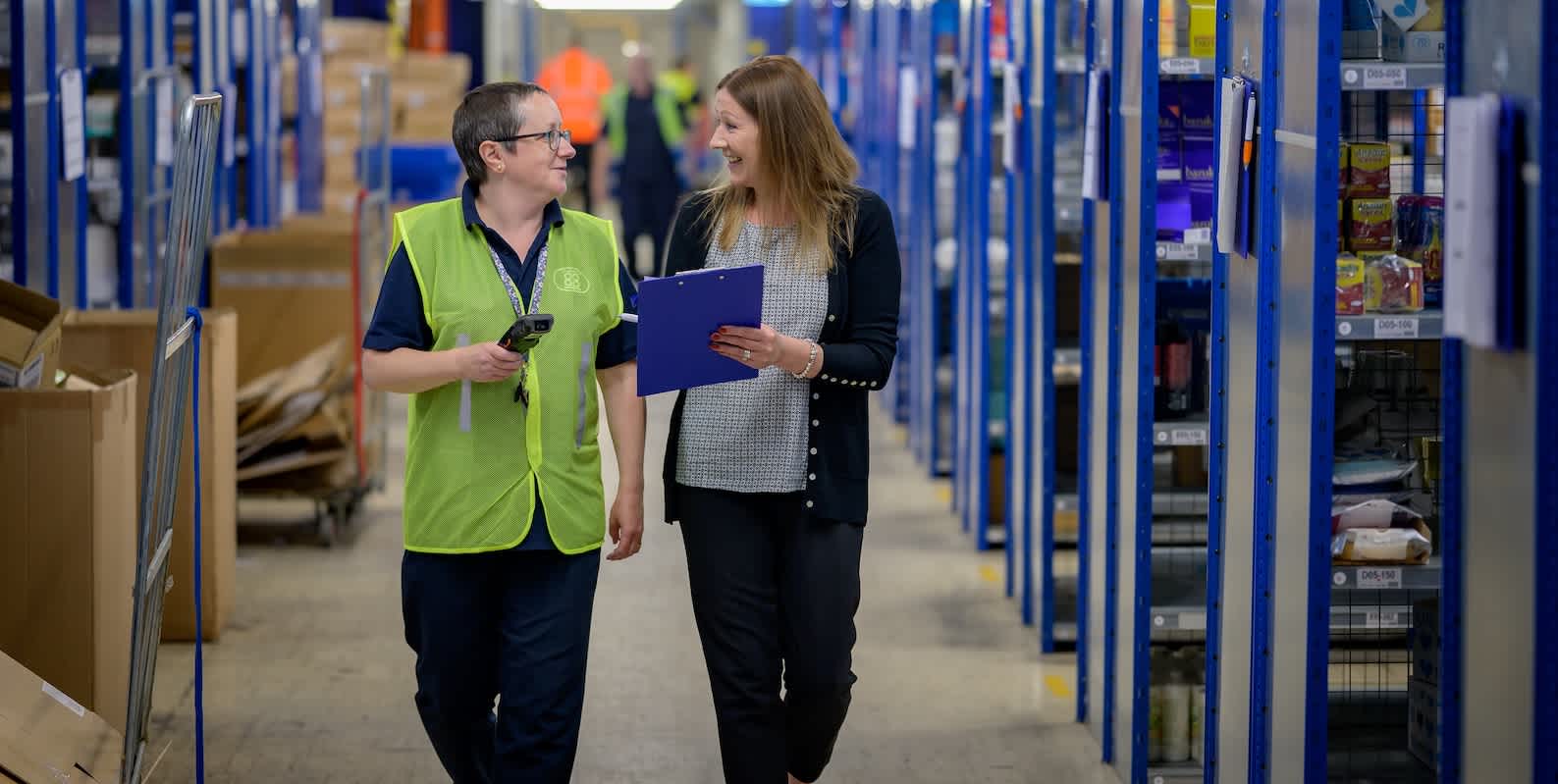
April 13, 2022
The Unknown Complexities of Inventory Compliance
The Unknown Complexities of Inventory Compliance
This article was originally published by Deliverr, which is now part of the Flexport brand. Its contents were edited to fit the voice and tone of the Flexport brand. With Deliverr’s services (DTC fulfillment, B2B distribution, and Last Mile delivery) now an integral part of Flexport’s end-to-end supply chain and technology capabilities, we’re able to arm merchants with logistics superpowers as a single entity of supply chain experts.
In order for any 3PL fulfillment service to be effective, it must be efficient. For a distribution operation to keep up with the demand of ecommerce, inventory must be properly packaged, labeled, and ready for the picking process. Your packaged products must adhere to guidelines to ensure a streamlined system of sending inventory to downstream fulfillment. This is known as inventory compliance.
Sending products to a fulfillment center is just the beginning of a series of considerations to guarantee your inventory is compliant. Whether you are relying on Amazon FBA or a third party, you must understand the complex nature of prepping your inventory to avoid being non-compliant among other things, such as:
- Being subjected to fines
- Incurring additional fees
- Refusal at the fulfillment center
- Returned inventory (at your brand’s expense)
- Prevention of future shipments
In addition, shipping costs, particularly overseas, are dependent upon pallet and container utilization. With this in mind, merchants often make the choice to mix SKUs and consolidate pallets. While this is extremely beneficial for a transportation CPU, it substantially raises the likelihood of your inventory being non-compliant.
Maintaining a well-oiled fulfillment system depends on inventory compliance with rules that not only protect products from damage during shipping but also ensure the safety of workers who handle the packages. Let’s take a look at the complexities of preparing inventory to meet these compliance standards to save your business time, money, and a huge headache.
Compliant Inventory Starts With Your Labels
Labels must be accurate and visible for warehouse workers for products to be identifiable and accounted for. This may seem like a no-brainer, but logistics providers have specific requirements to ensure inventory is properly labeled. Everything from placement, font type, and the printer used to produce labels is necessary to be compliant.
Moreover, package labels must include a shipment ID, scannable barcode, and ship-to and ship-from addresses. These labels must be on a flat side of the box or polybag and not on a corner, seam, or edge—and this is just for shipping labels to get your items accounted for upon arrival.
Various other labels are required for items to be considered compliant for downstream fulfillment, including:
- Sold as a set: To prevent products from being separated, items should be shrink wrapped together with a “Sold as a set” label affixed to the unit. This will avoid the separation of the products and allow the product to be scanned as a single item.
- Suffocation warning: Any polybag with an opening of 5 inches or more must have a suffocation warning label such as “To avoid any danger of suffocation, you must keep all plastic bags away from babies and children. Do not use these bags in cribs, beds, carriages, or playpens. These bags are not toys for kids to play with.” This must be printed in a legible font on the face of the packaging.
- Expiration date: Products with an expiration date must have a label with the date clearly visible in a font of 36 points or larger.
How to Ensure Compliance for Specific Items
Understand how your inventory needs to be prepped for fulfillment. Is your item fragile? Made of fabric? Considered a toy or baby product? Contain liquid? Any of these attributes leads to specific packaging guidelines.
Wrap Fragile and Glass Items
If your products are made of glass or another fragile material, they must be wrapped in bubble wrap or a protective box in order to comply. Items must pass a drop test on a hard surface without breaking. A scannable barcode must be affixed to the outside without needing to open the packaging in order to access it.
Protect Fabric and Cloth Items
Everything made of fabric, from apparel to textiles, must be packaged in a transparent bag with a suffocation warning and a scannable exterior barcode. This requirement prevents the products from being damaged by dust, dirt, or moisture throughout the downstream fulfillment process.
Show Warnings on Toys and Baby Products
Any item intended for a child three years or younger must be packaged in a transparent bag, and include a suffocation warning and a scannable barcode affixed to the outside of the bag. Similar to fabric items, this prevents any damage from dust, dirt, or liquid as it is handled in the fulfillment center.
Prevent Liquid Leaks
Liquids should ideally have a double seal to prevent leakage. Products such as soaps, cleaners, and perfumes should be packaged in a sealed bag with a suffocation label. A scannable barcode must be visible on the outside of the packaging without unwrapping.
But Wait, There’s More: Compliance for Box Specs and Their Contents
Boxes that arrive at fulfillment centers also endure scrutiny related to size, weight, and contents. Being well-versed in these requirements prevents your shipments from being turned away upon arrival.
Size and Weight
Boxes should not exceed 25 inches on any side. Boxes containing more than one item should be kept under 50 pounds. If a box containing a singly heavy item is between 50 and 100 pounds it should be clearly labeled as a “Team Lift.” If a box is over 100 pounds it should be labeled as “Mechanical Lift.”
Contents
Packing materials (aka dunnage) are also subject to varying compliance rules depending on the fulfillment provider. To meet FBA compliance, for example, inventory should not be shipped using packing peanuts, shredded paper, or other loose packing material. Instead, items should be packed with large sheets of kraft paper, air pillows, or sheets of bubble wrap or foam.
Avoid Costly Lost Cycles From Inventory Issues With Flexport’s Prep Services
Preparing inventory for downstream fulfillment takes time, energy, and planning to ensure items will remain intact and visible throughout the process. Complex guidelines protect products from damage and ensure worker safety during picking, packing, and shipping operations.
The expertise needed to oversee proper labeling, packaging, and materials, means brands rely on third-party logistics providers to handle the complex prep work for them.
Poorly prepped goods can cost you in provider rejections, non-compliance fees, damages, lost production cycles, and constrained inventory you can’t afford. With Flexport’s Prep services, we take on the complicated processes associated with preparing your products for downstream fulfillment so you can stop inventory issues before they happen.
So, the next time you’re questioning the status of your current inventory compliance, it may be time to consider switching 3PL fulfillment providers.
Related Content
PR Newswire
Flexport Acquires Shopify Logistics Expanding Its Global Services Into Last Mile and E-Commerce Fulfillment Becoming Their Official Logistics Partner